Brubaker Farms' methane digester expansion: a sustainable and cost-effective solution
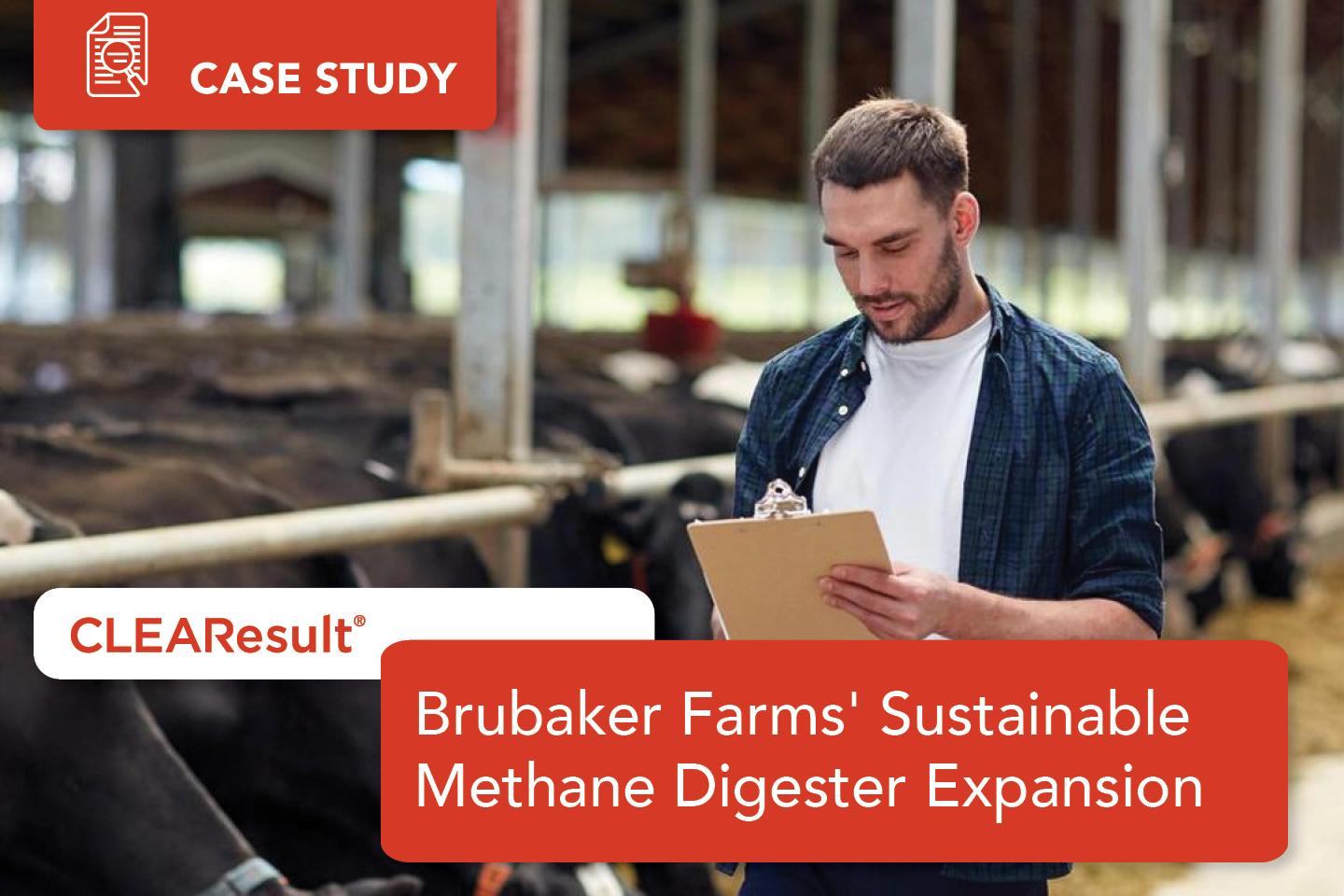
Project Quick Facts
2,644,000 kWh
estimated total annual savings
$80K
estimated total rebate savings
$798K
total project cost
3.5 Years
payback period
The Project
Brubaker Farms is a large dairy farm in Lancaster County, PA. It installed an anaerobic digestion manure management system to reduce odors and generate electricity for on-farm use due to the owner’s interest in sustainability.
The Opportunity
The farm’s anaerobic digester treated manure and generated electricity for over a decade, but reached the end of its lifespan sooner than anticipated, mostly due to wear and tear caused by the sulfurous methane gas. Rather than eliminating the system altogether, the farm decided to invest in new equipment, expanding its anaerobic digestion operation. The outgoing 223 kW engine generator was replaced with a 335 kW system, increasing their electrical generation capacity by 30%. Utility service had to be extended an extra mile down the lane to achieve such large capacity gains, driving up project costs. But thanks to utility incentives, the added costs were offset. What’s more, the farm added gas scrubbing equipment to increase the lifespan of the engine and improve the thermal recovery for milkhouse and water heating.
In the new system, methane is produced in a large storage tank by heating manure using waste heat from the engine generator. The gas scrubber then removes the sulfurous compounds before the gas passes through the engine used for electricity generation. Waste heat produced from the engine is captured during this process and reused for heating farm buildings and milk processing later.
The CLEAResult Difference
We tapped two subject matter experts in combined heat and power (CHP) and anaerobic digestion to help with the project’s planning measurement and verification (M&V). Our team provided a full M&V plan which was readily approved by the program evaluator. What’s more, our experts reviewed and utilized data from the existing daily production logs of the farm’s operational management system, thereby eliminating a burdensome extra step and the added expense of detailed monitoring.
The Results
The digester offsets utility costs of about $30,000 in electricity and $4,000 in natural gas annually by treating the manure generated by one thousand cows and food waste collected from a nearby college. The total cost of expanding the anaerobic digestion operation without incentives would take an estimated four years to pay back. Our work with evaluators to capitalize on the combined heat and power incentives cut the payback period to just three-and-a-half years.